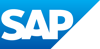
Boost competitiveness with Digital Manufacturing: more efficient processes and digital innovation
Sector
Industrial manufacturing
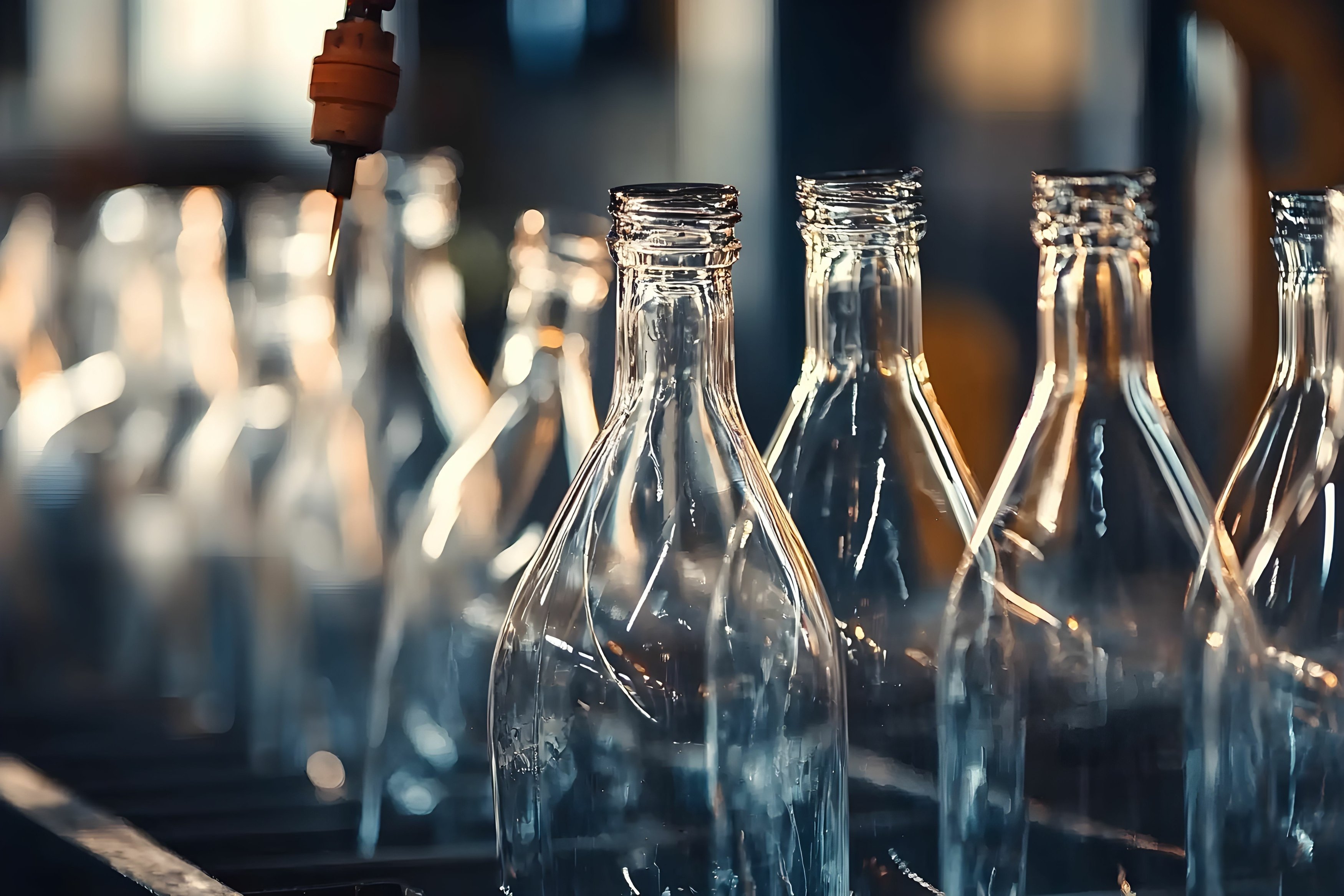
The customer
The client is a well-established Italian industrial company with a diversified portfolio of businesses operating across various sectors. At the heart of this project are two leading entities: a benchmark company in the production of glass containers for the food, cosmetics, and perfumery industries, and one of Italy’s largest alcoholic beverage producers.
The challenge
The Digital Manufacturing project was driven by the need to modernize and standardize production processes across the two companies involved, overcoming operational inefficiencies and technological limitations that hindered market competitiveness. The main challenge was to identify a single, flexible, and scalable solution capable of adapting to diverse needs while ensuring consistent management across the group’s various entities.
The Facilities
In the glass container manufacturer’s bottle decoration plant, production data collection, workflow tracking, and traceability still relied on paper-based processes. Meanwhile, the company’s Italian plants struggled with outdated and fragmented digital systems. For the alcoholic beverage producer, the key issue was inadequate pallet tracking, which negatively impacted production visibility and control.
In summary, the manufacturing environment required modernization and digitalization through a high-performance, unified system.
The solution & the benifts
The client has embarked on a three-year digital transformation project aimed at unifying and modernizing production processes on a global scale. Preparatory meetings, initiated at the end of 2023, led to the formalization of an implementation roadmap starting in March 2024, with the first deployment at the alcoholic beverage production facility. In September of the same year, a second project was launched, focusing on the glass container manufacturing plant. The goal is to create a flexible and shared technology platform capable of adapting to local specificities, improving real-time data access, and supporting more informed decision-making across all operational sites.
To achieve these objectives, the group has chosen SAP Digital Manufacturing (SAP DM) and SAP Business Technology Platform (SAP BTP), tools that address the needs of both sectors.
At the glass container manufacturing company, an advanced production monitoring system based on SAP DM is being implemented, enabling manual data collection and progress tracking. For the alcoholic beverage producer, the existing MES system has been replaced with a fully automated process, from pallet management to labeling and warehouse storage, thanks to integration with machine PLCs. This approach not only meets immediate operational needs but also lays the foundation for a modern and integrated digital management system capable of supporting the group’s future development.
The implementation provides the client with a fully integrated and multi-sector digital Manufacturing Execution environment, supporting the group’s operations on a global scale. The flexibility of the SAP BTP platform will enable the development of tailored solutions for the specific needs of glass production and alcohol bottling. With greater operational efficiency, market responsiveness, and real-time production visibility, the client will be able to reduce costs, optimize resources, and sustain international growth. The initiative aligns with their strategic objectives, aiming to standardize production processes and build a unified digital manufacturing platform.
ARE YOU ALSO EXPERIENCING THIS SITUATION?
Contact us to arrange a 15 minute call with our experts to see if we have the perfect solution for you